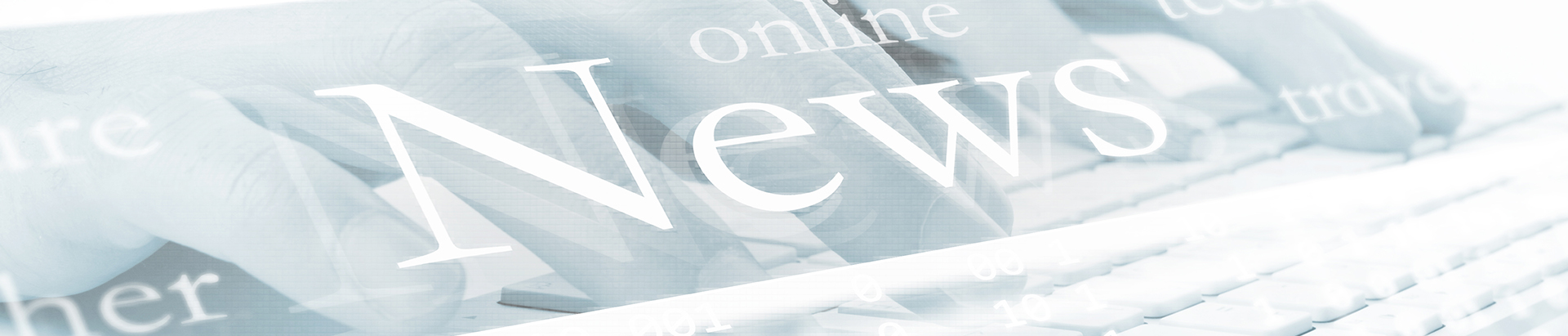
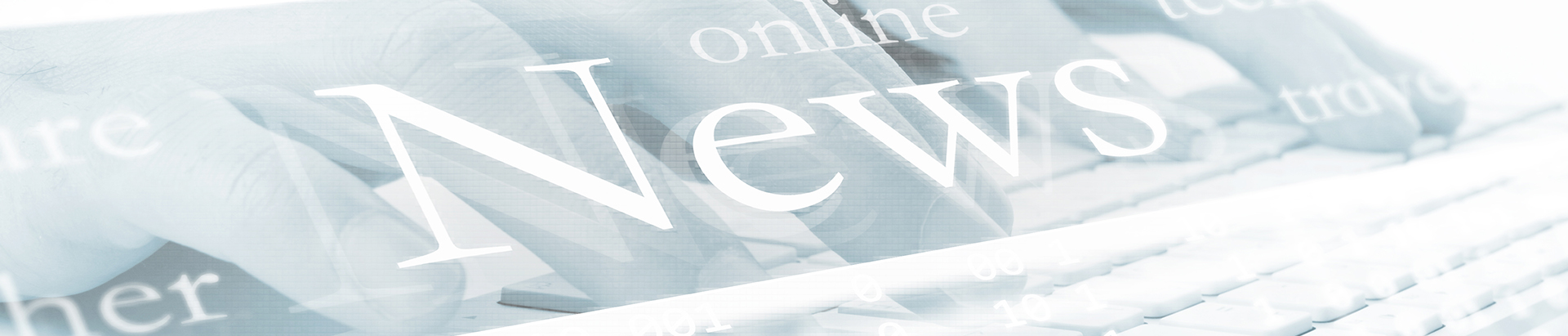
ADW has been actively expanding the international market, providing professional products and services for customers in many countries and regions around the world. in June, the company will participate in SENSOR+TEST, with advanced intelligent sensors and actuators and their solutions, to help the European region to upgrade the ‘smart manufacturing’.
SENSOR+TEST is one of Europe's largest sensor and test and measurement technology exhibitions and a major annual event for the global sensor and test and measurement technology industry.SENSOR TEST focuses on showcasing the latest in sensor technology, test and measurement equipment, automation technology, instrumentation, and other products and services.
ADW Booth Information
Date: 11 - 13 June 2024
Venue: Germany - Nuremberg Exhibition Centre
Booth number: 1-521
Part of the products display
Flexible Pressure Sensor
Flexible pressure sensor is a new type of pressure sensitive element with wide range, high sensitivity and high pressure resolution, compared with traditional pressure sensors, it has higher sensitivity, more stable signal and strong cycling reliability; the product uses micro-structure design, complete with small size, short response time, wide pressure response range and other high strength application functions. At the same time, the product has both static force and dynamic force detection capabilities, showing great potential for application in many fields such as medical care, rescue, and precision operations.
- Flexibility to adapt to dynamically changing surfaces
- Wearable, can be attached to skin, clothing or other objects.
- Highly integrated, can be integrated with other sensors to form complex sensing systems.
- Micro-structure design, small size, light weight
- High sensitivity, both static force and dynamic force detection capability.
Piezoelectric Jetting Valve
The Piezoelectric Jetting Valve is a dispensing component for precise control of fluids such as adhesives, paints, inks, etc. The internal core actuator is deformed by the inverse piezoelectric effect when energized to push the internal piston or diaphragm to achieve precise control of the fluid. The product eliminates Z-axis movement, which prevents the needle from colliding with the work-piece and effectively improves productivity and yield.
- Maximum operating frequency 3000Hz
- Minimum spray volume 1nL
- Suitable for colloids with viscosity ≤ 500,000 mPa.s.
- Modular design, small valve size
- No Z-axis movement, avoid needle collision with work-piece, high yield.
Piezoelectric Stack
Piezoelectric stack is a multi-layers piezoelectric ceramics formed by co-firing multiple piezoelectric ceramic films through the hot press bonding process, which uses the inverse piezoelectric effect to convert electrical energy into mechanical energy, the product has a high-resolution, high-precision displacement, fast response speed, small size, large force and other advantages, in high-precision valve control, micro-displacement console and other fields are widely used.
- Highly accurate displacement in microns
- Millisecond response time
- Small size, high output
- Wide range of operating temperatures, suitable for multiple scenarios
Ultrasonic motor
Ultrasonic motors are mainly composed of stator piezoelectric ceramics and rotor friction materials, etc. Using the inverse piezoelectric effect of piezoelectric ceramics, they generate elliptical vibrations in the ultrasonic frequency domain on the surface plasmas of the stator, and drive the rotor to rotate through contact friction between the rotor and the stator. The products are suitable for driving high-speed autofocus axes, digital microscopes, wafer inspection stages, as well as various types of carrier stages such as electron beam and ion beam carriers, spectroscopy carriers, and multi-axis carriers.
- Small size and light weight
- Fast reaction speed and good control characteristics
- Nano-scale control accuracy
- Self-locking when work stops, no heat generation.
- No electromagnetic interference, suitable for strong magnetic fields and other harsh working environments.
Haptic Feedback Actuator
Haptic feedback actuators use piezoelectric haptic feedback technology, through the physical principle of positive and negative piezoelectric effect for intelligent terminals to reproduce the real sense of touch. When the driving voltage is loaded to the haptic feedback actuator, the part produces mechanical deformation, so it causes vibration within a limited range, such as the application of the product in mobile phones can replace the old mechanical button interface with high-resolution local haptic buttons, and reshape the interaction mode of the intelligent terminal.
- Low power consumption, 10 times more energy efficient than mechanical technology
- Small size, support multi-channels design
- IP68 level protection, highly waterproof, dustproof, oilproof, anti-pollution.
- Supports multi-dimensional interaction with multiple synchronisation, multiple interfaces and multi-functions.
- Advanced seamless design, effectively simplify the whole machine industrial design, keep the lines smooth and beautiful.